Настя
Offline
| Дата: Среда, 23.11.2011, 21:18 | Сообщение # 1
|
Модераторы
Сообщений: 157
| ПОВЫШЕНИЕ ЖЕСТКОСТИ КЛЕТЕЙ И ТОЧНОСТИ РАЗМЕРОВ ПРОКАТА Повышение точности размеров проката - источник значительной эконо¬мии металла1. 1 О целесообразности повышения точности размеров прокатки можно судить из следующего примера. Для горячекатаных листов толщиной 4-10 мм поле допусков по ГОСТу составляет 10-25 % толщины. Благодаря улучшению конструкции стана и повышению точности прокатываемых листов поле допусков можно уменьшить вдвое и получить при той же площади прокатываемых листов экономию металла в 4,4 %. Современные конструкции и системы регулирования прокатных станов поз-воляют резко повысить точность прокатываемых изделий. Упорядочив допуски на прокат, изготовленный на новых станах, можно получить за счет использования отрицательного поля допусков экономию металла порядка 350 тыс. т в год. Главными направлениями повышения точности прокатки можно считать: для листового и полосового проката - применение систем автоматического регулирования межвалкового расстояния и систем регулирования противоизгиба валков с целью получения листов с высокой точностью по геометрии (разнотолщинность, плоскостность); для сортовых профилей - использование напряженных клетей при одновременном устранении или регулировании натяжения. Применение наиболее эффективных систем автоматического регулирования, действующих по принципу измерения толщины до и после прокатки, натяжения перед клетью и после нее (при холодной прокатке) и усилий при прокатке, позволяет существенно повысить точность прокатки на листовых станах. При этом проблема повышения жесткости прокатных клетей должна отступить на второй план. Разработанные за последние годы приборы для измерения ширины полосы позволяют решать задачу повышения точности указанных размеров на основе ав-томатического регулирования расстояния между валками. Повышение точности прокатки сортовых и, главным образом, сложных профилей не всегда достигается автоматическим регулированием межвалкового расстояния. Поэтому одновременно с разработкой надежных приборов и систем ав-томатического регулирования размеров профиля, аналогично полосовым станам, повышение точности прокатки применительно к сортовым станам должно осуще-ствляться с использованием предварительно напряженных или жестких клетей. При этом можно существенно (в 1,5-2 раза) сократить поле допусков и получить экономию металла (в 1-2 %). Упругая деформация рабочей клети Под воздействием усилия прокатки возникают упругие деформации элементов рабочих клетей: станин, валков, подшипников, нажимных устройств и др. В результате этих деформаций установленный зазор между валками изменяется. При прокатке тонких листов изменение величины зазора может быть соизмеримо не только с допусками на готовый прокат, но и с его конечной толщиной. Причины, вызывающие изменение толщины полосы, могут быть разнообразные: неравномерность толщины по ширине и длине подката, непостоянство условий смазки в процессе прокатки, эксцентриситет (биение) валков, колебание натяжений, неравномерность механических свойств прокатываемого металла, прогиб и упругое сплющивание валков, износ поверхностей бочек и др. На точность прокатки, кроме вышеперечисленных факторов, оказывает вли-яние и динамика процесса прокатки. Самый простой способ повышения жесткости прокатных клетей листовых станов - это увеличение диаметра валков и поперечного сечения станины. Однако чрезмерное возрастание жесткости может привести к тому, что биение опорных валков (эксцентриситет) будет отрицательно сказываться на качестве проката вследствие возникновения продольной разнотолщинности. Поэтому следует добиваться снижения эксцентриситета в результате обработки бочек и шеек опорных и рабочих валков на современных, более точных станках. Продольная разнотолщинность листового проката в значительной степени зависит от скорости прокатки, при ее снижении (прохождение сварных швов, про-катка заднего конца полосы) масляный клин на ПЖТ выдавливается и зазор меж-ду валками увеличивается, при ее повышении - наоборот. Поперечная разнотолщинность зависит от непосредственного прогиба и сплющивания валков, а также от наследственной разнотолщинности и механиче-ских свойств по ширине подката и других факторов. Силовая профилировка валков Эффективным средством борьбы с поперечной разнотолщинностью можно считать силовую профилировку (противоизгиб) рабочих или опорных валков. На практике существуют три способа силовой профилировки валков (рис. 1.34). 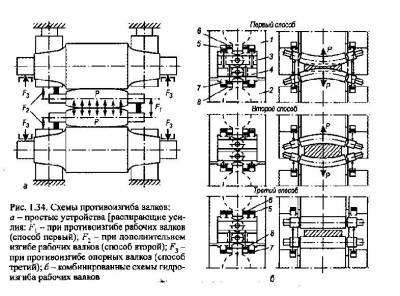
|
|
| |
Настя
Offline
| Дата: Среда, 23.11.2011, 21:18 | Сообщение # 2
|
Модераторы
Сообщений: 157
| Первый способ - осуществление противоизгиба рабочих валков. Валки имеют цилиндрическую форму или небольшую выпуклую бочку. Прогиб валков под действием усилия Р уменьшается в результате принудительного противоизгиба рабочих валков при приложении распирающих усилий 2F1 к их шейкам. Гидравлические цилиндры 5-8 размещены в расточках подушек нижнего рабочего валка 4, а их плунжеры упираются в подушки верхнего рабочего валка 3. Усилие гидрораспора небольшое (0,15Р), поэтому и габариты устройства невелики (диаметр цилиндров 80ч100 мм при давлении жидкости до 30 МПа). Данное устрой-ство осуществляет также функцию уравновешивающего. Наиболее оптимальный противоизгиб рабочих валков является при соотношении ширины бочки и ее длины b/l< 0,7. Второй способ - дополнительный изгиб рабочих валков, имеющих бочку увеличенной выпуклости. Гидроцилиндры расположены в подушках опорных валков 1 и 2, а их плунжеры опираются на подушки рабочих валков. Дополнительно к прогибу от действия усилия Р рабочие валки дополнительно изгибаются в том же направлении силами 2F2 = 0,2Р. При дополнительном изгибе профиль бочки валка становится прямым. Способ наиболее эффективен при прокатке широ¬кой полосы (b/l = 0,8ч0,9). На практике применяют также комбинированную сис¬тему, позволяющую использовать оба способа. Третий способ - противоизгиб опорных валков. Опорные валки принудитель¬но изгибаются силами 2F3 = Р, уменьшая прогиб рабочих валков. В случае противоизгиба опорных валков требуются значительные усилия, для восприятия кото¬рых на консольных цапфах требуется устанавливать крупногабаритные ролико¬вые подшипники. Гидроцилиндры имеют тоже большие размеры и усложняют конструкцию клети. На рис. 1.34, б показано изменение профиля поперечного сечения полосы при различных схемах приложения усилий к подушкам (шейкам) рабочих валков без учета прогиба валков под действием усилия прокатки Р при комбинированной схеме изгиба рабочих валков четырехвалковых клетей. В некоторых случаях снижению поперечной разнотолщинности способствует профилировка валков. В общем случае можно отметить, что оптимальная жесткость клети достигается соответствующим выбором размеров станины, диаметра валков, подшипников жидкостного трения. Определяется жесткость в зависимости от прокатываемого сортамента, требуемой точности размеров полосы, а также возможностей автоматического регулирования толщины полосы и других параметров прокатки.
|
|
| |